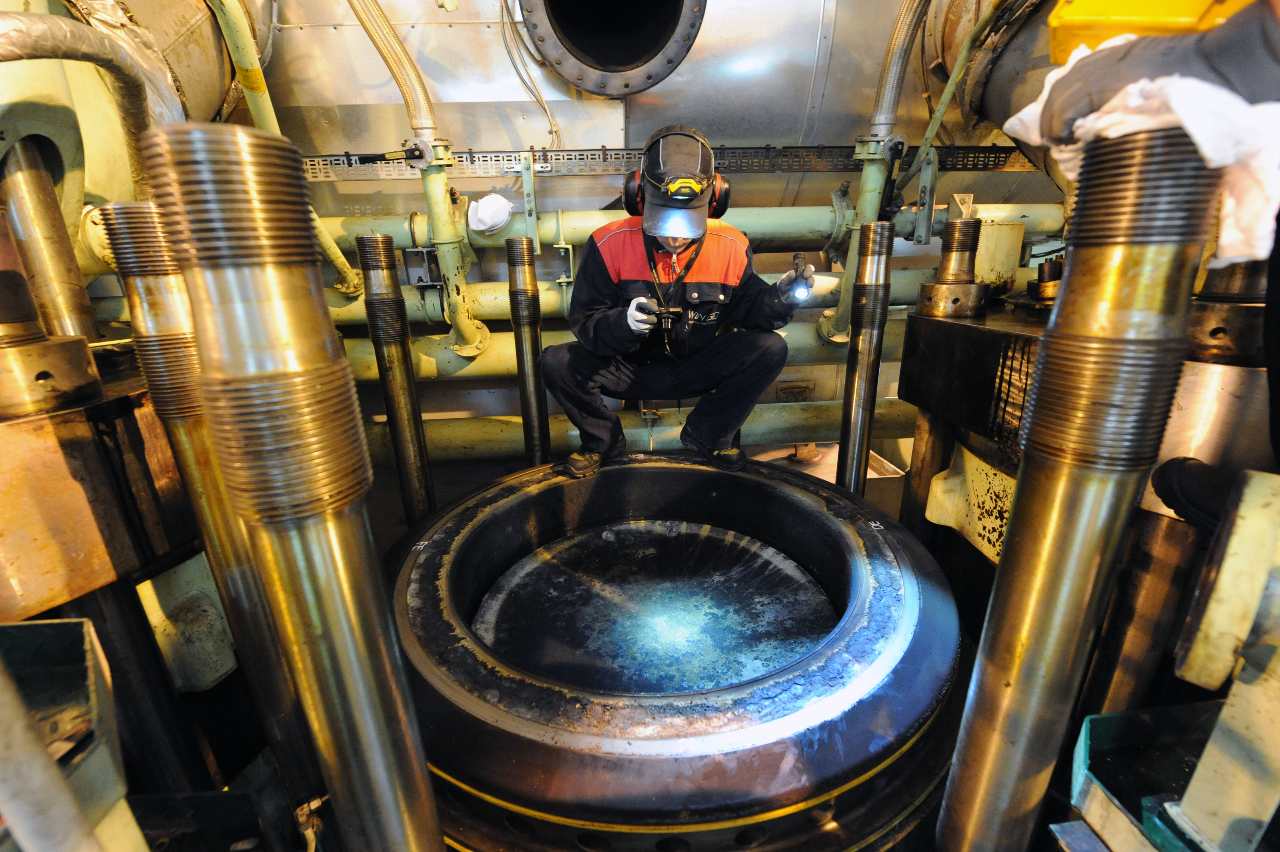
Getting the right balance of lubricant feed rate whilst achieving optimum performance is the goal operators seek to achieve. The use of low sulfur fuels under IMO2020 and modern engines designs mean greater attention needs to be given to achieving the right balance to maintain engine performance.
In our white paper - Adapting to Life in the Post IMO2020 Landscape – we look at the issues that both under and over lubrication can bring and the benefits of optimum lubrication, which we discuss in this blog.
Vessel operators understand very well that under lubrication is dangerous in the long run as there is not enough active matter from the lubricant injected into the engine.
Less recognized however are the issues associated with over lubrication, which can potentially lead to excessive deposits and engine scuffing, not to mention costly repair. Not only are modern engines particularly sensitive to corrosion and corrosive wear, but also engines burning inconsistent VLSFO fuel batches through IMO2020 further increases the risk of deposit build up.
Optimizing the Engine Lubrication Feed Rate
Achieving the right level of two-stroke engine cylinder lubrication offers multiple benefits for vessel operators including OPEX control and increased safety margins. Yet, all too many still suffer from the problems associated with under or over lubrication.
Under Lubrication
Key issues associated with under lubrication include insufficient engine protection resulting in increased, or even excessive, liner wear. Under lubrication will also result in insufficient active matter to deliver suitable acid neutralization and detergency to help keep the engine clean.
Over Lubrication
It is often wrongly assumed that over lubrication will not damage the engine. The reality is that excessive lubrication can also create problems, which can be extremely costly. One of the biggest issues of over lubrication is the excess amount of unused lubricant, which can result in increased carbon deposits. Over time these deposits increase, leading to carbonization, ultimately creating a barrier between the fresh oil and the piston liner enhancing the potential risk of ‘scuffing’.
This poses a serious threat to operations and OPEX, resulting not only in an operator paying more for their lubrication usage but increasing the risk of damage and repair costs.
Optimum Lubrication
Optimum lubrication can only be achieved through a dedicated lubrication monitoring and management programme. Drain oil analysis programmes are easy to integrate, helping optimize operations through lubrication consumption and component wear analysis with a number of support and technical programmes to choose from.
By taking this supported approach, vessel operators can see the key benefit of consistent engine cleanliness without engine deposit build up, preventing costly engine damage, downtime and repair.