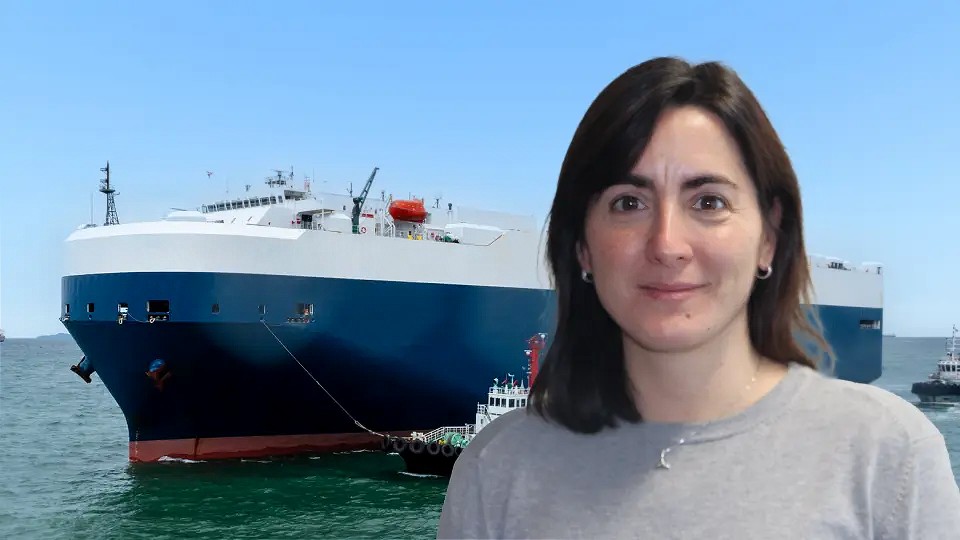
Having taken up the newly created role of Supply Chain Manager- Upstream within Lubmarine’s Safety and Supply Chain Division, Maria Garay has not only changed her job but her life, moving from her homeland of Argentina where she worked with TotalEnergies for the last 16 years, to Paris.
Here she shares her experiences within TotalEnergies and outlines the challenges that lie ahead in harmonizing Lubmarine’s global supply chain.
This is a really exciting new role – Can you tell us your route to it?
I guess you could say I have been working my way towards this role for the last 16 years since I first started working with TotalEnergies.
My first role with the Company started in Argentina. Having studied foreign trade at University it is safe to say I fell in love with international logistics and studied supply chain at Post Graduate Level.
I began as an assistant in the Foreign Trade Department working within our blending plant in La Tablada, a city in the Greater Buenos Aires metro area.
Within a few years I had worked my way up and I was in charge of the purchasing department.
Not only was I in charge of the purchases for the lubricants activity but also for LPG activity that we had back then within Argentina. I had two teams – one working with imports and exports. The other team included category managers in charge of purchasing different goods and services such as transport and all types of goods, services and consumables for the blending plant.
We had to ensure that we were purchasing within the Company’s established processes. It was a young team and I really enjoyed working with them.
We had a great group and positive environment and whilst there was a lot of pressure I learned the importance of generating a good working environment. It was a dynamic place to work and it was a great place to work. I thought that I was going to be in purchasing forever!
But I was then offered to move into operations as planning manager – overseeing planning for the blending plant as well as the warehouse operations. It was a role I enjoyed for three years from 2016-2019.
Argentina is in a geographically challenging location from a planning perspective and we introduced demand planning with the commercial teams and what we managed to achieve was integrating key processes across departments within the Company.
We had to introduce planning processes across the business that had not previously been in place so you can imagine the related challenges. But what I was really pleased about was that the ideas and processes we introduced made a positive difference.
In January 2020 I was appointed Production and Maintenance Manager at the blending plant, the biggest blending plant in the region with a capacity to produce 50,000 tons per year of lubricants, greases and coolants.
I was in charge of production, a 100% operational role and a role I really enjoyed. Being near the teams and understanding their needs and by doing so, identifying how we could make improvements in terms of productivity and also within their working roles. The approach turned out well and we introduced the 5-S lean manufacturing methodology (Sort, Set in order, Shine, Standardize, and Sustain).
It was great because the teams were very enthusiastic and by fully involving them in the change process they could see and feel the differences being made and therefore we could initiate further changes because they had experienced positive impacts.
When I started working in that role I wondered how I could make a difference and I was able to bring experience in management and building teams and seeing how collectively as a team we could make the changes we needed to.
Can you tell us more about your new role?
Having spent all my life living and working in Argentina, I spotted the new role of Supply Chain Manager – Upstream, which was going to be based in Paris. One of my life dreams has been to work and live abroad and I really wanted to go for it!
The role was created because the global crisis that impacted supply chains in recent years, due to logistics constraints and COVID pandemics restrictions, among other reasons, proved how executing a really effective supply chain is a major priority playing a massively important role in meeting the needs of our customers worldwide. An efficient supply chain is a must!
Along with my colleague in Asia, Alexandra Wong, our role really is at a strategic level - to seek to guarantee supply to all of our blending plants. Lubmarine has around 55 plants around the world - we have our own TotalEnergies plants and affiliates and partners who blend for us so it is a big network.
We know the goals we need to achieve and my role is working out how we achieve them.
Can you tell us about some of the key challenges within the role?
I love challenges and this is certainly a challenging role. Within our network of 55 plants we have eight major ones and we work very closely with them to ensure they have everything they need to operate efficiently.
It’s a complex web as we are dealing with different companies (not just our own blending plants), different ways of working and different time zones and that means we have a lot of complexities to seek to harmonize.
Our goal is to create a situation where we are in full control of our blending capabilities, stock levels and all associated criteria on a global level, and to have visibility on that by putting in place different reports.
Some of the key words for us are robustness and agility. It’s about having the right product, at the right time where and when the customer needs it. And the supply chain is central to this.
And it all starts with knowing where we are with our plants and stocks around the world.
Another main challenge is related to risk management, where we analyze and set contingency plans in the supply field. And of course we constantly seek to contribute in different efficiencies and costs.
What are you enjoying about the role despite the fact it is still relatively early days?
It is great to be able to go out and meet the teams in the blending plants where we are looking to adopt efficiencies and to discuss what we are trying to do and how that will bring benefits to them.
Working closely with the teams in the blending plants is essential if we are going to reach our goals of being in a position to always ensure supply, always have visibility – on both stock and logistics and always having a ‘Plan B’ - for all of our supply chain risks.
Ultimately we are looking to harmonize our work across the world wherever we can along with establishing KPIs and reports.
When you are not working what do you like to do?
My focus lies with my family. Because we have just moved to Paris we are looking to make connections, friends and interests. At weekends we try to travel to get to know France better and enjoy where we are.
I have 2 kids (aged 4 and 8) so I didn’t think that moving from Argentina to France would be possible. But the move has been great. The children are adapting really well and love living here. It has been easier than we thought to get used to living in France. The people have been very welcoming.
I also love scuba diving so I like to do this as much as I can. We always plan our holidays so we can get into the water!
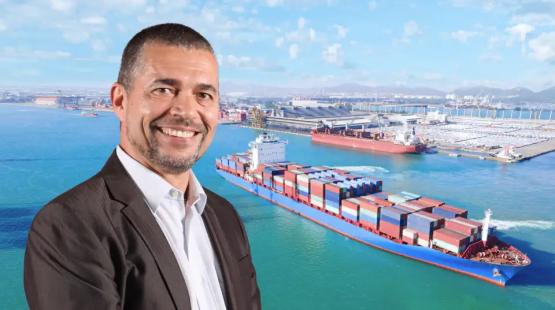

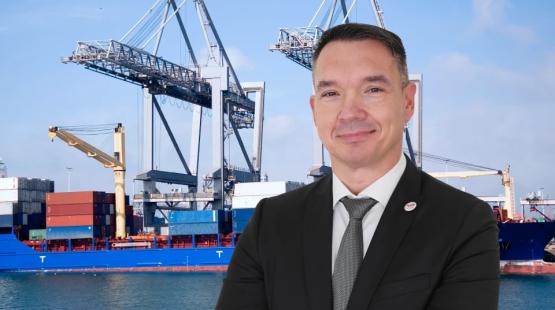